Iron Ore Magnetite
The key economic parameters for magnetite ore being economic are the crystallinity of the magnetite, the grade of the iron within the banded iron formation host rock, and the contaminant elements which exist within the magnetite concentrate. The size and strip ratio of most magnetite resources is irrelevant as a banded iron formation can be hundreds of meters thick, extend hundreds of kilometres along strike, and can easily come to more than three billion or more tonnes of contained ore.
The typical grade of iron at which a magnetite-bearing banded iron formation becomes economic is roughly 25% iron, which can generally yield a 33% to 40% recovery of magnetite by weight, to produce a concentrate grading in excess of 64% iron by weight. The typical magnetite iron-ore concentrate has less than 0.1% phosphorus, 3–7% silica and less than 3% aluminium.
Currently magnetite iron ore is mined in Middle East,Australia& Canada Magnetite bearing banded iron formation is currently mined extensively in Brazil, which exports significant quantities to Asia, and there is a nascent and large magnetite iron-ore industry in Australia.
We can supply Iron ore from lower grade of 40% Fe to 65% Fe.
Magnetite is magnetic, and hence easily separated from the gangue minerals and capable of producing a high-grade concentrate with very low levels of impurities
The grain size of the magnetite and its degree of commingling with the silica groundmass determine the grind size to which the rock must be comminuted to enable efficient magnetic separation to provide a high purity magnetite concentrate. This determines the energy inputs required to run a milling operation.
Mining of banded iron formations involves coarse crushing and screening, followed by rough crushing and fine grinding to comminute the ore to the point where the crystallized magnetite and quartz are fine enough that the quartz is left behind when the resultant powder is passed under a magnetic separator.
Generally most magnetite banded iron formation deposits must be ground to between 32 and 45 micrometers in order to produce a low-silica magnetite concentrate. Magnetite concentrate grades are generally in excess of 70% iron by weight and usually are low phosphorus, low aluminium, low titanium and low silica and demand a premium price.
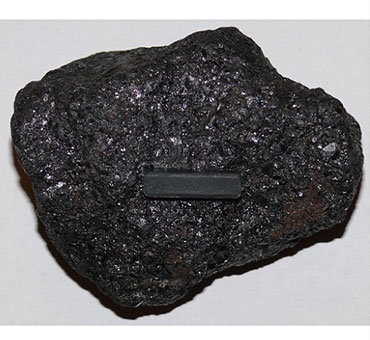
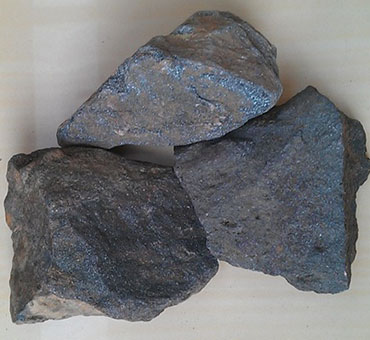
Iron Ore Hematite
Due to the high density of hematite relative to associated silicate gangue, hematite beneficiation usually involves a combination of beneficiation techniques.
One method relies on passing the finely crushed ore over a slurry containing magnetite or other agent such as ferrosilicon which increases its density. When the density of the slurry is properly calibrated, the hematite will sink and the silicate mineral fragments will float and can be removed.
We can supply good quantities of Iron ore from India,Middle East and CIS countries.
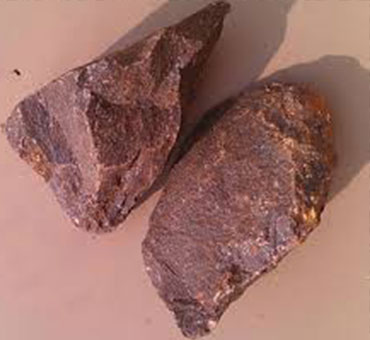
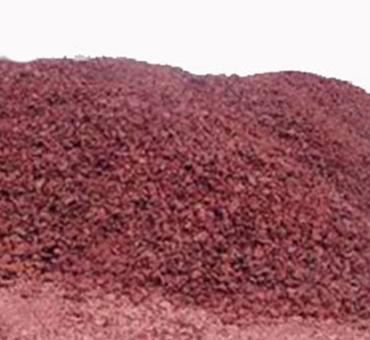
Direct reduced iron (DRI)
Direct reduced iron (DRI), also called sponge iron, is produced from the direct reduction of iron ore (in the form of lumps, pellets, or fines) to iron by a reducing gas or elemental carbon produced from natural gas or coal. Many ores are suitable for direct reduction.
Reduced iron derives its name from the chemical change that iron ore undergoes when it is heated in a furnace at a high temperature of 800 to 1200 °C in the presence of a reducing gas called syngas which is a mixture of hydrogen and carbon monoxide.
Direct reduction refers to processes which reduce iron oxides to metallic iron at temperatures below the melting point of iron. The product of such solid state processes is called direct reduced iron.
Direct reduction processes can be divided roughly into two categories: gas-based, and coal-based. In both cases, the objective of the process is to drive off the oxygen contained in various forms of iron ore (sized ore, concentrates, pellets, mill scale, furnace dust, etc.), in order to convert the ore to metallic iron, without melting it (below 1200 °C).
The direct reduction process is comparatively energy efficient. Steel made using DRI requires significantly less fuel, in that a traditional blast furnace is not needed. DRI is most commonly made into steel using electric arc furnaces to take advantage of the heat produced by the DRI product.
Benefits :In modern times, direct reduction processes have been developed to specifically overcome the difficulties of conventional blast furnaces. DRI is successfully manufactured in various parts of the world. The initial investment and operating costs of direct reduction plants are low compared to integrated steel plants and are more suitable for developing countries where supplies of coking coal are limited.
Factors that help make DRI economical :Direct-reduced iron has about the same iron content as pig iron, typically 90–94% total iron (depending on the quality of the raw ore) so it is an excellent feedstock for the electric furnaces used by mini mills, allowing them to use lower grades of scrap for the rest of the charge or to produce higher grades of steel.
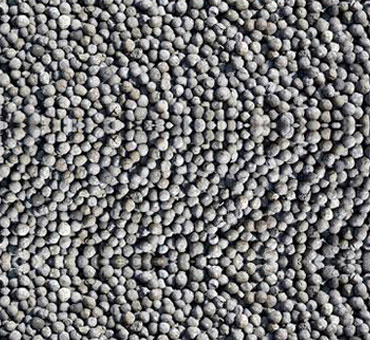
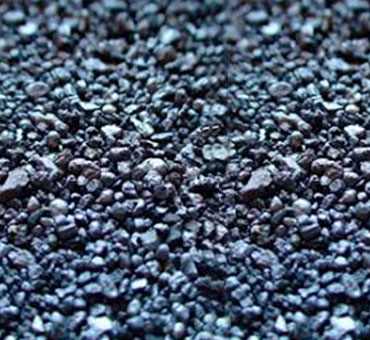
Hot-briquetted iron (HBI)
Hot-briquetted iron (HBI) is a compacted form of DRI designed for ease of shipping, handling and storage. Hot direct reduced iron (HDRI) is iron not cooled before discharge from the reduction furnace, that is immediately transported to a waiting electric arc furnace and charged, thereby saving energy. The direct reduction process uses pelletized iron ore or natural "lump" ore. One exception is the fluidized bed process which requires sized iron ore particles.
The direct reduction process can use natural gas contaminated with inert gases, avoiding the need to remove these gases for other use. However, any inert gas contamination of the reducing gas lowers the effect (quality) of that gas stream and the thermal efficiency of the process.
Supplies of powdered ore and raw natural gas are both available in areas such as Northern Australia, avoiding transport costs for the gas. In most cases the DRI plant is located near natural gas source as it is more cost effective to ship the ore rather than the gas.
This method produces 97% pure iron.
India is the world’s largest producer of direct-reduced iron, a vital constituent of the steel industry.[4] Many other countries use variants of the process, so providing iron for local engineering industries.
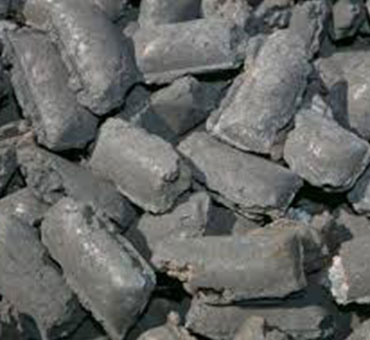
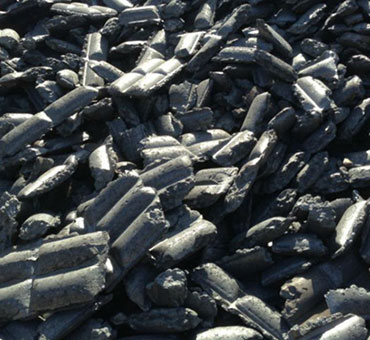